Unser früherer Allrounder, das beliebte KNX-Bedienpanel Controlmini, wurde rein entwicklungstechnisch völlig neu konzipiert. Das Interview mit Gerald Palmsteiner, unserem Head of Product Management, zeigt, wie der Weg zum neuen Endprodukt und der damit einhergehenden Namensänderung aussah.
Was war der Ausgangpunkt für die Neuentwicklung?
Der ursprüngliche Anstoß zur Systemumstellung basierte auf rein pragmatischen Gründen: Verfügbarkeit von Teilen, Beständigkeit unserer Produkte und Erhöhung der Leistungsfähigkeit. Die eigentliche technische Umstellung des Panels bezieht sich überwiegend auf die „inneren Werte“. Rein optisch wird der Kunde am Panel wenig von der Überarbeitung merken, denn der Rahmen, das Full-HD Display und die USB-Frontanschlüsse bleiben. Nur an den austauschbaren Frontgläsern sind neue Ausschnitte für Sensoren und eine LED hinzugekommen. Was sich aber durchaus ändert, ist unsere Visualisierung YOUVI. Darauf gehen wir später noch näher ein.
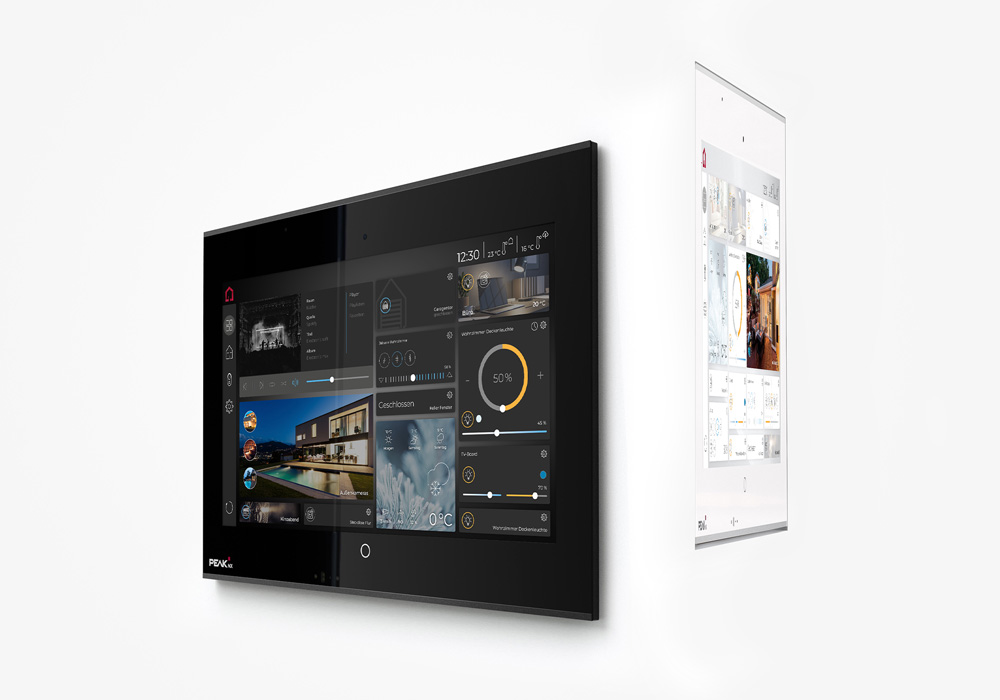
Und es gibt einen neuen Namen. Warum haben Sie sich für die Änderung entschieden, obwohl der Name Controlmini bereits etabliert war?
Die Entscheidung fiel während des Umstellungsprozesses. Für unsere Kunden wird es leichter, sich innerhalb unserer Panelfamilie zu orientieren. Vor allem, wenn noch weitere Größen dazu kommen sollten. Außerdem sind die technischen Unterschiede im Inneren des neuen Panels im Vergleich zur Vorgängerversion so groß, dass wir das als Anlass genommen haben, dem Kind einen neuen Namen zu geben – Control 12.
Um auf die drei Gründe für die technische Umstellung zurückzukommen: Können Sie uns diese Gründe näher erläutern?
Durch die globalen Krisen der letzten Jahre ist es immer schwerer geworden, benötigte Bauteile in der gewohnt guten Qualität und innerhalb angemessener Lieferfristen zu bekommen. Produktionszyklen ziehen sich mehr und mehr in die Länge. Allein schon deswegen sahen wir uns gezwungen, alte Bahnen zu verlassen. Zulieferer neigen heutzutage dazu, gewisse Baugruppen „on demand“ zu produzieren oder erst, wenn die Bestellmenge ein gewisses Volumen erreicht. Dann erst wird die Einkaufsabteilung beim Zulieferer aktiv, um sich die entsprechenden Rohstoffe zu besorgen. Wenn aber etwas gerade nicht verfügbar ist, kann auch nicht produziert werden. Es war daher wichtig für uns, unabhängiger von Zulieferern zu werden.
Einen Teil der Problematik konnten wir lösen, indem wir den Anteil an Eigenentwicklung erhöht haben. So sind wir beispielsweise weggegangen von kompletten Bauteilen hin zu Teilen, die wir selbst zusammenbauen konnten und deren Funktionen wir selbst entwickelt haben. Man kann das mit einem Hausbau vergleichen: Wir kaufen jetzt nicht mehr die kompletten Elemente für ein Fertighaus, sondern nehmen einzelne Steine und bauen sie entsprechend zusammen.
Was die Beständigkeit unserer Produkte angeht, so ist es von jeher unser Anspruch gewesen, die Panels so zu konstruieren, dass sie eine sehr lange Lebensdauer aufweisen und eine geringe Ausfallquote haben. Wir glauben, dass wir mit der neuen Generation dieses Vorhaben noch weiter optimiert haben. In dem Zusammenhang konnten wir das Thema Wartung und Reparatur optimieren, da jetzt noch mehr aus eigener Entwicklung kommt. Falls trotz der Langlebigkeit unserer Produkte mal etwas defekt sein sollte, können wir unseren Kundinnen und Kunden eine unkomplizierte Wartung bzw. Reparatur bieten. Das war bisher zwar auch schon immer der Fall, aber jetzt kommen wir damit zusätzlich dem in diesem Jahr eingereichten Gesetzesvorschlag der EU-Kommission zum Thema „Recht auf Reparatur“ nach. Darin wird das Recht von Kundinnen und Kunden auf Reparatur ihrer defekten Geräte gefordert. Letztendlich werden insgesamt viel zu viele Produkte entsorgt, die eigentlich noch gebrauchsfähig wären und repariert werden könnten. Wir tragen also mit unseren hochwertigen Produkten auch zur Reduzierung von Elektroschrott und zu mehr Nachhaltigkeit bei.
Zum Punkt der Leistungsfähigkeit lässt sich sagen, dass nach unserer Philosophie unsere Panels nicht nur reine Bedienpanels sind, sondern Multimediazentralen mit einem vollumfänglichen Windows OS. Wir wollen natürlich den steigenden Ansprüchen unserer Kunden gerecht werden und mit der Zeit gehen. Kameras werden immer hochauflösender, unsere Visualisierung YOUVI anspruchsvoller und wenn diverse Anwendungen gleichzeitig laufen, konnte das Gerät kapazitätsmäßig in der Vergangenheit schon mal an seine Grenzen stoßen. Das konnten wir durch die Veränderung des Innenlebens beim neuen Modell des früheren Controlminis ausräumen. Wir haben die Leistungsfähigkeit des Geräts verbessert, das Panel noch zukunftsfähiger gemacht und sind für steigende Leistungsansprüche bestens gerüstet. Mit dem schnelleren 128-Gigabyte-Hauptspeicher sind wir auch für den Wechsel auf Windows 11 vorbereitet, sobald eine Version mit Langzeitunterstützung zur Verfügung steht.
Welcher der Punkte hat Sie vor die größte Herausforderung gestellt?
Letztendlich war es ein Mix aus allen. Um die Performance und die Qualität noch mehr zu steigern, mussten wir uns um den schon erwähnten Einkauf neuer Komponenten kümmern, ohne aber die gestiegenen Einkaufspreise an den Kunden weitergeben zu müssen. Der Fokus lag jedoch vor allem auf der Steigerung der allgemeinen Leistungsfähigkeit und auf der Lösung der damit einhergehenden Probleme.
Könnten Sie das etwas näher beschreiben?
Nun, wir wussten, dass wir neue Wege gehen müssen, um das Gerät leistungsfähiger und qualitativ noch hochwertiger und langlebiger zu machen. Die Herausforderung bestand zum einen darin, auf sehr wenig Platz viel Leistung unterzubringen. Denn potenziell soll die Technologie auch bei kleineren Geräten anwendbar sein.
Ein anderes großes Thema war das Wärmemanagement bzw. die Energieeffizienz. Das Gerät soll im absoluten Sparmodus laufen, wenn es nur als Lichtschalter verwendet wird, aber bei Multimediaanwendungen soll es die Leistung anheben. Wir brauchten ein neues Entwicklungskonzept, um entstehende Hitze während solcher Leistungsspitzen abzufangen, ohne auf einen Lüfter zurückgreifen zu müssen. Schon allein deshalb konnte es keine vorgefertigte Lösung geben und es war wesentlich mehr eigene Entwicklungsarbeit geboten. Wir haben es aber geschafft, durch die neue Konfiguration die Wärmeentwicklung und somit den Verbrauch im Normalbetrieb reduzieren. Das bedeutet höhere Effizienz, also mehr Leistung bei geringerem Verbrauch. Und gleichzeitig stehen mehr Leistungsreserven zur Verfügung.
Mehr eigene Entwicklungsarbeit war auch für den modularen Aufbau im Inneren des Geräts nötig. Durch die erhöhte technische Modularität sind wir bereit, zukünftig einfacher Änderungen z. B. bei der Konfiguration der Festplatte oder an einzelnen Komponenten wie dem Prozessor durchführen zu können. Auch dann, wenn es sich um eine zwischenzeitlich veraltete Prozessorgeneration handelt. Die modulare Technik sorgt also für die oben angesprochene größere Langlebigkeit der Geräte.
Welche verschiedenen Schritte gab es bei der Entwicklung?
Da gab es natürlich, wie bei jeder Produktentwicklung, unterschiedliche Phasen. Von der Ist-Zustand-Analyse, über die Recherche und den Bau verschiedener Prototypen inklusive Tests bis hin zur Serienfertigung. Erstmal mussten wir über interne und externe Quellen herausfinden, was bis dahin am aktuellen Gerät gut funktioniert, also weiterverwendet werden kann bzw. was optimiert werden sollte und die Anforderungen nach Priorität in einem Lastenheft festlegen. Darauf basierend haben wir recherchiert, welche Lösungen es auf dem Markt gibt und was wir selbst entwickeln und fertigen können. So haben wir die Weichen für die Entwicklungsrichtung gestellt.
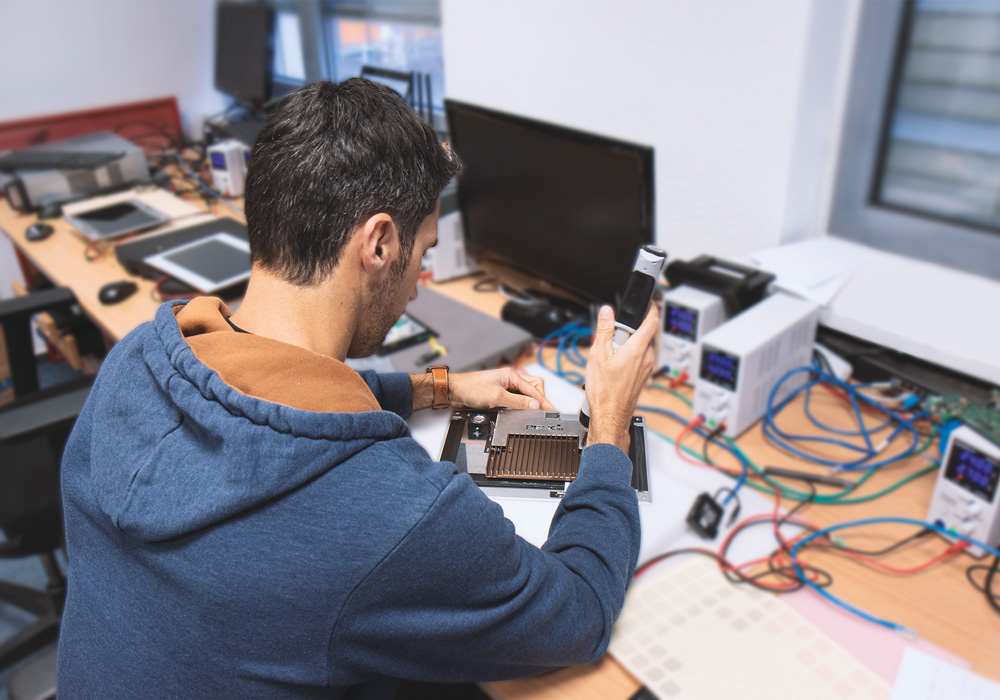
Richtig spannend wurde es dann bei der Entwicklung der Prototypen. Unser erster Prototyp wich vom Aufbau her zwar noch stark vom anvisierten Endprodukt ab, aber wir bekamen durch verschiedene Tests grundsätzlicher Funktionen von Einzelkomponenten wichtige Erkenntnisse, konnten Fehler beheben und tatsächlich erste Komponenten für die Serie bestellen.
Unser zweiter Prototyp kam dem geplanten Prototyp in Größe, Aufbau und bei der Position der wichtigsten Komponenten schon viel näher. Fehler, die beim ersten Prototyp aufgetaucht waren, wurden gefixt, wir führten Belastungstests und erste interne CE-Tests durch. Am Ende konnten wir das Gerät für die Serienproduktion optimieren und die restlichen Komponenten bestellen. Das war der Startschuss für die Serienproduktion.
Die letzte Phase wurde durch den Aufbau von Nullserienmodellen eingeleitet, damit wir die gesamte Funktionsfähigkeit verifizieren konnten. Und dann, nach den internen und externen CE-Tests für die erforderlichen Zertifizierungen, gaben wir grünes Licht für die Serienfertigung. Was uns natürlich mächtig stolz gemacht hat.
Gab es bei dieser Umstellung auch etwas, mit dem Sie nicht gerechnet haben und das sich auf den Zeitplan ausgewirkt hat?
So einiges. Aber um alles zu erklären, würde das hier den Rahmen sprengen. Das größte Thema war hierbei das Wärmemanagement bzw. die Energieeffizienz.
Mit dem Zeitplan sprechen Sie einen wunden Punkt an. Um ihn einzuhalten, mussten wir uns mächtig ins Zeug legen. Jedes unerwartete Problem, jedes negative Testergebnis und jeder zusätzliche Wunsch der Geschäftsleitung während der genannten Entwicklungsphasen musste nach hinten raus kompensiert werden. Man darf auch nicht vergessen, dass wir mit der kompletten Neuentwicklung ein Risiko eingegangen sind. Denn wir wussten nicht, ob das alles zusammen so funktioniert, wie wir es uns vorgestellt haben und ob wir die notwendigen Bauteile in der richtigen Stückzahl immer rechtzeitig bekommen.
Am Ende war es eine starke Teamleistung aus unseren Entwicklern und unserer Schwesterfirma PEAK-System Technik. Die Kolleginnen und Kollegen dort haben uns sehr dabei geholfen, unser Ziel zu erreichen. Denn schließlich konnten wir firmenintern vor Ort auf ein über 30-jähirges Know-how zu Elektronik- und Platinenentwicklung zurückgreifen.
Gab es Veränderungen bei der Hardware?
Wie schon erwähnt, wurde das Panel optisch von vorne nur geringfügig verändert. Lediglich beim Frontglas gibt es Veränderungen: Aufgrund neuer Sensorik sind einige neue Ausschnitte hinzugekommen. Ein Helligkeitssensor regelt die automatische Anpassung der Helligkeit an die Umgebung und ein Distanzsensor erkennt, wenn sich eine Person dem Display nähert und schaltet dann automatisch den Bildschirm ein. Außerdem gibt es eine Benachrichtigungs-LED an der Vorderseite, die individuell mit Funktionen belegt werden kann. Frontanschlüsse, Rahmen und Lautsprecher sind identisch zur Vorgängerversion des Panels. Auch die bisher verwendeten Einbaurahmen können problemlos weitergenutzt werden. Das neue Gerät ist weiterhin kompatibel mit den alten Aufputz-Rahmen oder Unterputz-Dosen und Adaptersets.
Im Inneren ist jedoch kein Stein auf dem anderen geblieben. Die Hauptplatine haben wir von Grund auf neu entwickelt, die modulare Technik bietet mehr Flexibilität, z. B. bei der Verteilung der Anschlüsse. Es kommt ein neuer Prozessor zum Einsatz, beim Hauptspeicher wurde sowohl die Kapazität als auch die Geschwindigkeit erhöht. Im hinteren Innenbereich befindet sich eine neue USB-C-Schnittstelle und per Ethernet sind nun Übertragungsraten im Gigabitbereich möglich. Auch die Datenübertragung per LAN, WLAN bzw. Bluetooth wurde auf den aktuellen Stand der Technik gebracht.
"Bei den Spezifikationen konnten wir in allen Bereichen zulegen und gleichzeitig das Wärmemanagement optimieren. Insgesamt sorgt das Ergebnis unserer Arbeit für eine noch höhere Beständigkeit des Panels. Was will man mehr?"
Und wie hat sich die Visualisierungssoftware YOUVI verändert?
Unsere YOUVI zeigt sich künftig in einem neuen, noch klareren Design. So gibt es eine veränderter Farbgebung, die überwiegend in blau und gelb gehalten ist, bei den Widgets sind Bilder mit einbezogen und die verschiedenen Anwendungsbereiche sind über neu gestaltete Buttons jetzt noch besser ansteuerbar. Natürlich kann die neue Version von YOUVI - wie schon in der Vergangenheit - in dunklem oder hellen Modus verwendet werden. Außerdem sind einige neue Features zu Benutzermanagement, Klimatisierung oder auch Sound hinzugekommen.
Sind Sie mit dem Endergebnis Ihrer Arbeit zufrieden?
Definitiv! Wir haben viel geschafft, auf das wir stolz sein können: Das System ist noch effizienter geworden, da es jetzt noch mehr auf die Bedürfnisse der Kunden bzw. deren Anwendung eingeht. Die Visualisierungssoftware wurde weiterentwickelt und die Leistungsfähigkeit des Panels konnte in den Bereichen Festplatte, Prozessor und Grafikkarte um bis zu 300 % gesteigert werden. Den Gesamtbenchmark konnten wir um etwa 150 % erhöhen. Bei den Spezifikationen konnten wir in allen Bereichen zulegen und gleichzeitig das Wärmemanagement optimieren. Insgesamt sorgt das Ergebnis unserer Arbeit für eine noch höhere Beständigkeit des Panels. Was will man mehr?
Das neue Panel ist seit Anfang 2024 auf dem Markt und bisher hatten wir von Kundenseite durchweg positives Feedback! Das konnten wir auch live auf der Light + Building erfahren. Lesen Sie dazu gerne unseren Light + Building Blogbeitrag.