Our former allrounder, the popular KNX control panel Controlmini, has been undergone a complete overhaul in terms of development. The interview with Gerald Palmsteiner, our Head of Product Management, illustrates the journey towards the new product and the change in name.
What was the impetus for the redevelopment?
The impetus for the system overhaul was purely pragmatic: availability of parts, durability of our products, and increasing performance. The actual technical transition of the panel mainly concerns its "inner workings". Visually, the customer will notice little change to the panel, as the frame, Full HD display, and front USB ports remain unchanged. Only on the interchangeable front glasses, new cutouts for sensors and an LED have been added. However, what does change is our visualisation software, YOUVI. We'll delve into that in more detail later on.
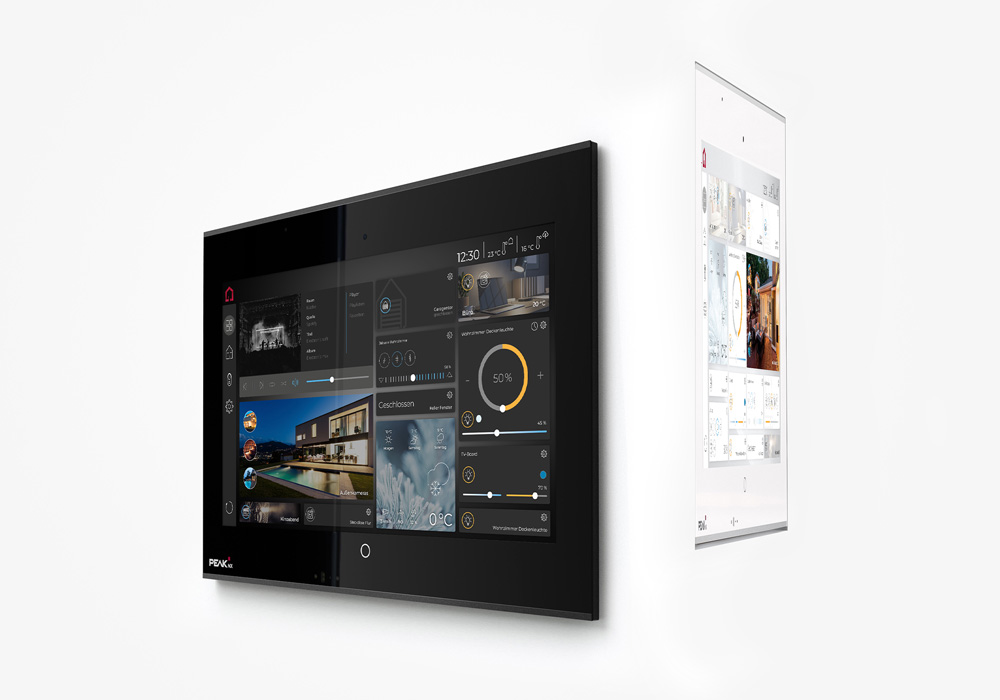
And there's a new name. Why did you decide to change it even though the name Controlmini was already established?
The decision was made during the transition process. For our customers, it will be easier to navigate within our panel family. Especially if additional sizes are added later on. Furthermore, the technical differences inside the new panel compared to the previous version are so significant that we took it as an opportunity to give the product a new name – Control 12.
To pick up on the three reasons for the technical transition: Could you please explain these reasons in more detail?
Due to the global crises of recent years, it has become increasingly difficult to obtain the required components in the accustomed high quality and within reasonable delivery times. Production cycles are stretching longer and longer. For these reasons alone, we felt compelled to depart from old practices. Nowadays, suppliers tend to produce certain assemblies "on demand" or only when the order quantity reaches a certain volume. Only then does the purchasing department at the supplier become active to source the necessary raw materials. However, if something is currently not available, production is not possible. Therefore, it was important for us to become more independent from suppliers.
We were able to solve part of the problem by increasing the proportion of in-house development. For example, we have decided to no longer purchase complete components, but to acquire parts that we can assemble ourselves and whose functions we developed in-house. This can be compared to building a house: we no longer purchase the complete elements for a prefabricated house, but instead, we take individual bricks and assemble them accordingly.
Regarding the durability of our products, it has always been our goal to design the panels in a way that ensures a very long lifespan and low failure rate. We believe that with the new generation, we have further optimized this endeavour. In this context, we were able to improve maintenance and repair aspects, as development is more and more our own part. If, despite the longevity of our products, something is defective, we can offer our customers straightforward maintenance or repair services. While this has always been the case, we are now additionally complying with the EU Commission's proposed legislation on the "Right to Repair," submitted last year. This legislation calls for the right of customers to repair their defective devices. Ultimately, far too many products are discarded that could still be used and repaired. Therefore, with our high-quality products, we also contribute to reducing electronic waste and promoting sustainability.
Regarding the performance, it is our philosophy that our panels are not just mere control panels, but multimedia centres with a comprehensive Windows OS. Of course, we aim to meet the increasing demands of our customers and stay up-to-date. Cameras are becoming increasingly higher-resolution, our visualisation software YOUVI is becoming more sophisticated, and when various applications run simultaneously, the device could sometimes reach its capacity limits in the past. In the new model of the former Controlmini we have addressed this issue by changing the internal components. We have improved the device's performance, made the panel even more future-proof, and are well-prepared for increasing performance demands. With the faster 128-gigabyte main memory, we are also prepared for the transition to Windows 11 once a long-term support version becomes available.
Which of the points posed the greatest challenge for you?
Ultimately, it was a mix of all aspects. To further enhance performance and quality, we had to procure new components, as mentioned earlier, without passing on the increased purchasing prices to the customer. However, the main focus was on improving overall performance and addressing the associated challenges.
Could you elaborate on that?
Well, we knew we had to chart new paths to make the device more powerful and even higher in quality and durability. The challenge lay in fitting a lot of power into a very small space. After all, the technology should potentially be applicable even in smaller devices.
Another major issue was thermal management or energy efficiency. The device should run in an absolute low-power mode when used only as a light switch, but it should increase performance for multimedia applications. We needed a new development concept to handle the heat generated during such performance peaks without relying on a fan. Therefore, we did not want a pre-made solution, and much more in-house development work was required. However, we managed to reduce heat generation and thus consumption in normal operation through the new configuration. This means higher efficiency, i.e., more performance with lower consumption. And at the same time, more power reserves are available.
More in-house development work was also necessary for the modular design inside the device. With increased technical modularity, we are prepared to make future changes more easily, such as configuring the hard drive or individual components like the processor. This holds true even if it involves an outdated processor generation. Thus, the modular technology ensures the greater longevity of the devices as mentioned earlier.
What were the different steps in the development process?
Of course, as with any product development, there were different phases involved. From the analysis of the current state, through research and the construction of various prototypes including testing, to serial production. Firstly, we had to determine through internal and external sources what worked well on the current device up to that point, meaning what could be reused or what needed optimization, and prioritize the requirements in a specification sheet. Based on this, we researched what solutions were available on the market and what we could develop and manufacture ourselves. This set the direction for the development process.
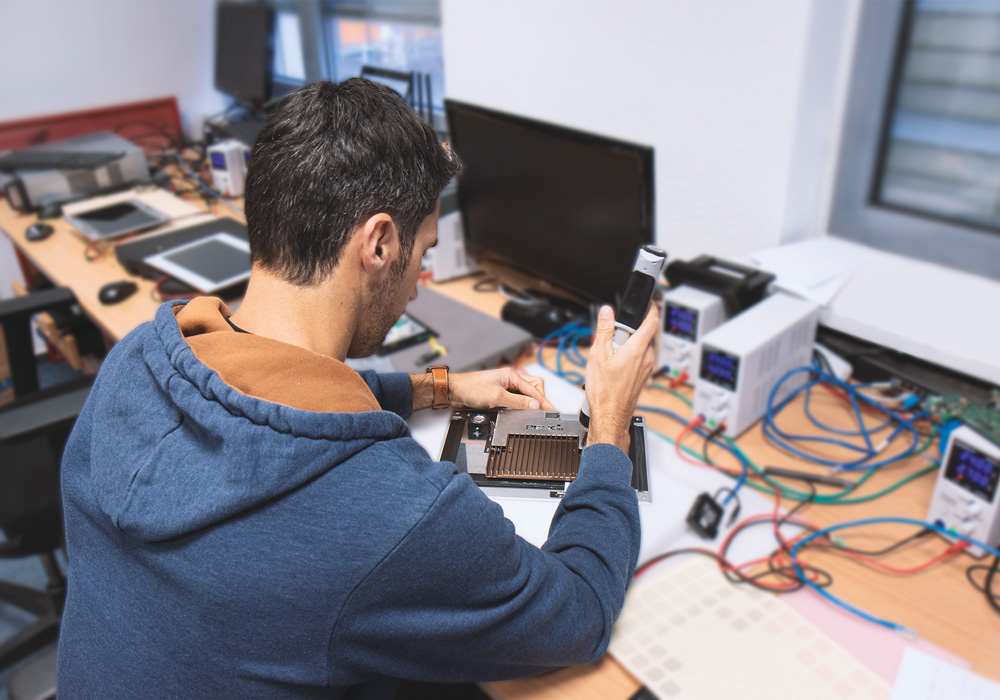
The development of prototypes was particularly exciting. Although our first prototype differed significantly in structure from the intended end product, various tests of basic functions of individual components provided important insights. We were able to identify and rectify errors, and actually order the first components for mass production.
Our second prototype closely resembled the planned prototype in size, structure, and the positioning of key components. Errors encountered in the first prototype were rectified, and we conducted stress tests and initial internal CE tests. In the end, we were able to optimize the device for mass production and order the remaining components. This marked the start of serial production.
The final phase began with the construction of pre-production models, allowing us to verify the entire functionality. Following internal and external CE tests for the necessary certifications, we gave the green light for mass production. This, of course, made us incredibly proud.
Did anything unexpected occur during this transition that affected the timeline?
Quite a few things, actually. But to explain everything would be beyond the scope here. The biggest issue was indeed the thermal management or energy efficiency.
You've hit a sore spot by mentioning the timeline. To adhere to it, we had to really push ourselves. Every unexpected problem, every negative test result, and every additional request from management during the mentioned development phases had to be subsequently made up for. It's also important to remember that with the complete redesign, we took a risk. We didn't know if everything would work together as we envisioned it, and whether we would always receive the necessary components in the right quantity on time.
In the end, it was a strong team effort from our developers and our sister company, PEAK-System Technik. The colleagues there greatly assisted us in achieving our goal. After all, we were able to draw on over 30 years of in-house expertise in electronics and PCB development.
Where there any changes to the hardware?
As mentioned earlier, the panel has undergone only minor cosmetic alterations on the front. The only changes occured with the front glass: due to new sensors, some new cutouts have been added. A brightness sensor adjusts the brightness automatically according to the surroundings, and a distance sensor detects when a person approaches the display, automatically turning on the screen. Additionally, there is a notification LED on the front that can be individually assigned functions. Front connectors, frames, and speakers are identical to the previous version of the panel. The existing mounting frames can also be easily reused. The new device remains compatible with the old surface-mounted frames or flush-mount boxes and adapter sets.
However, internally, everything has been revamped. We have completely redesigned the mainboard, and the modular technology offers more flexibility, for example, in the distribution of connections. A new processor is being used, and both the capacity and speed of the main memory have been increased. A new USB-C interface is located in the rear interior, and with Ethernet, transmission rates in the gigabit range are now possible. Data transmission via LAN, WLAN, or Bluetooth has also been updated to the latest technology standards.
"We've improved in all areas of specifications while simultaneously optimizing heat management. Overall, the result of our work ensures an even higher durability of the panel. What more could one expect?"
How has the visualisation software YOUVI changed?
Our YOUVI visualisation now boasts a new, even clearer design. This includes a modified colour scheme, predominantly featuring blue and yellow tones, with images incorporated into the widgets. The various application areas are now even more accessible through newly designed buttons. Naturally, the new version of YOUVI, as in the past, can be used in either dark or light mode. Additionally, several new features related to user management, climate control, and sound have been added.
Are you content with the result of your work?
Absolutely! We've achieved a lot that we can be proud of: The system has become more efficient, as it now caters even more to the needs of customers and their applications. The visualisation software has been further developed, and the performance of the panel has been increased by up to 300% in areas such as hard drive, processor, and graphics card. We've been able to increase the overall benchmark by about 150%. We've improved in all areas of specifications while simultaneously optimizing heat management. Overall, the result of our work ensures an even higher durability of the panel. What more could one expect?
The new panel has been on the market since the beginning of 2024, and so far, we've received consistently positive feedback from customers! We also experienced this firsthand at the Light + Building trade fair. Feel free to read our blog post about Light + Building as well.