Notre ancien polyvalent, le panneau de commande KNX très apprécié Controlmini, a été complètement repensé du point de vue du développement. L'interview avec Gerald Palmsteiner, notre responsable de la gestion des produits, montre comment le chemin vers le nouveau produit final et le changement de nom qui en découle se sont déroulés.
Quel a été le point de départ de cette nouvelle conception ?
Le point de départ initial pour la transition du système reposait purement sur des raisons pragmatiques : disponibilité des pièces, durabilité de nos produits et amélioration des performances. La transition technique réelle du panneau se concentre principalement sur ses "éléments internes". Du point de vue visuel, le client remarquera peu de changements sur le panneau, car le cadre, l'écran Full HD et les ports USB en façade restent inchangés. Seuls de nouveaux découpes pour les capteurs et une LED ont été ajoutés aux vitres frontales interchangeables. Cependant, ce qui change vraiment, c'est notre visualisation YOUVI. Nous y reviendrons plus en détail plus tard.
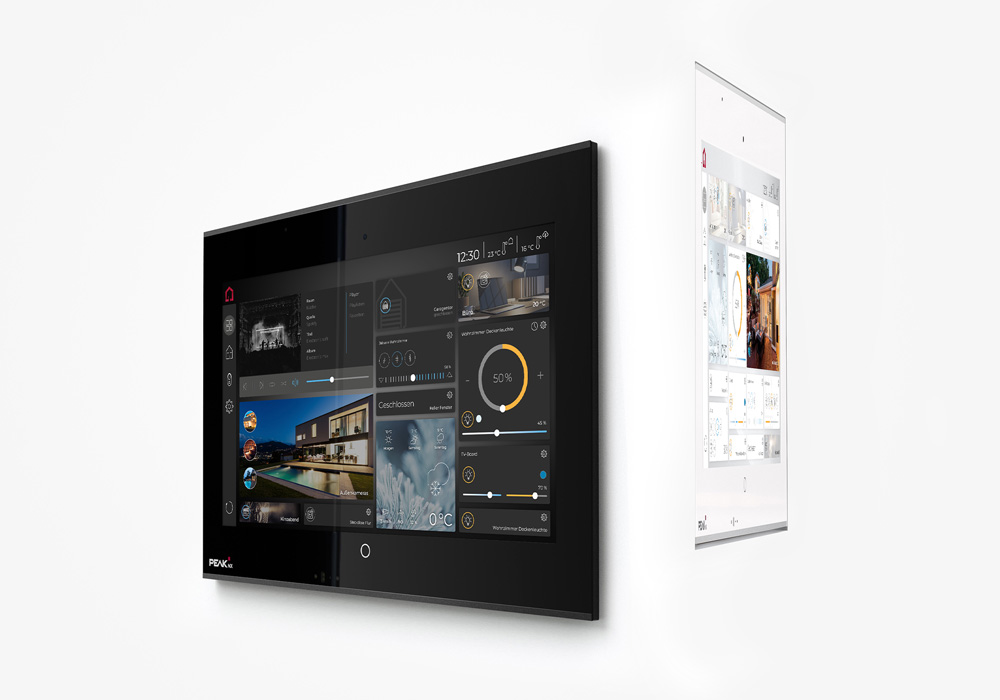
Et il y a un nouveau nom. Pourquoi avez-vous décidé de changer, alors que le nom Controlmini était déjà établi ?
La décision a été prise pendant le processus de transition. Pour nos clients, il sera plus facile de s'orienter au sein de notre famille de panneaux. Surtout si d'autres tailles devaient être ajoutées à l'avenir. De plus, les différences techniques à l'intérieur du nouveau panneau par rapport à la version précédente sont si importantes que nous avons saisi l'occasion de lui donner un nouveau nom - Control 12.
Pour revenir aux trois raisons de la transition technique : Pouvez-vous nous expliquer ces raisons plus en détail ?
Les crises mondiales des dernières années ont rendu de plus en plus difficile l'obtention des composants nécessaires dans la qualité habituelle et dans des délais de livraison raisonnables. Les cycles de production s'allongent de plus en plus. Pour cette raison, nous avons été contraints de sortir des sentiers battus. De nos jours, les fournisseurs ont tendance à produire certaines pièces "à la demande" ou seulement lorsque la quantité commandée atteint un certain volume. Ensuite, le département des achats du fournisseur entre en action pour se procurer les matières premières nécessaires. Cependant, si quelque chose n'est pas disponible, la production ne peut pas avoir lieu. Il était donc important pour nous de devenir moins dépendants des fournisseurs.
Nous avons résolu une partie de ce problème en augmentant la part du développement interne. Par exemple, nous sommes passés de l'utilisation de pièces complètes à des pièces que nous pouvions assembler nous-mêmes et dont nous pouvions développer les fonctions. Cela peut être comparé à la construction d'une maison : nous n'achetons plus les éléments complets d'une maison préfabriquée, mais nous prenons des briques individuelles et les assemblons en conséquence.
En ce qui concerne la durabilité de nos produits, il a toujours été notre objectif de concevoir les panneaux de manière à ce qu'ils aient une longue durée de vie et un faible taux de défaillance. Nous pensons avoir encore optimisé cette ambition avec la nouvelle génération. À cet égard, nous avons pu optimiser la maintenance et la réparation, car encore plus de composants proviennent de notre propre développement. Si malgré la durabilité de nos produits, un dysfonctionnement survenait, nous pouvons offrir à nos clients un service de maintenance ou de réparation sans complications. Bien que cela ait toujours été le cas jusqu'à présent, nous nous conformons également à la proposition de loi soumise l’année dernière par la Commission européenne concernant le "droit à la réparation". Ce texte demande le droit des consommateurs à faire réparer leurs appareils défectueux. Au final, trop de produits parfaitement utilisables sont jetés alors qu'ils pourraient être réparés. Ainsi, avec nos produits de haute qualité, nous contribuons également à réduire les déchets électroniques et à promouvoir la durabilité.
En ce qui concerne les performances, selon notre philosophie, nos panneaux ne sont pas simplement des panneaux de commande, mais des centres multimédias avec un système d'exploitation Windows complet. Nous voulons bien sûr répondre aux exigences croissantes de nos clients et suivre l'évolution du temps. Les caméras deviennent de plus en plus haute résolution, notre visualisation YOUVI plus exigeante, et lorsque plusieurs applications sont en cours d'exécution simultanément, l'appareil pouvait parfois atteindre ses limites de capacité par le passé. Nous avons résolu ce problème en modifiant l'architecture interne du nouveau modèle du précédent Controlmini. Nous avons amélioré les performances de l'appareil, rendu le panneau encore plus adapté à l'avenir et nous sommes bien préparés pour répondre aux exigences de performance croissantes. Avec une mémoire principale plus rapide de 128 gigaoctets, nous sommes également prêts pour la transition vers Windows 11 dès qu'une version avec support à long terme sera disponible.
Quel point vous a posé le plus grand défi ?
Finalement, c'était un mélange de tous les aspects. Pour améliorer encore davantage les performances et la qualité, nous avons dû nous occuper de l'achat de nouveaux composants, sans pour autant répercuter les prix d'achat plus élevés sur les clients. Cependant, l'accent était surtout mis sur l'augmentation des performances générales et sur la résolution des problèmes qui en découlent.
Pourriez-vous détailler un peu plus ?
Nous savions que nous devions emprunter de nouvelles voies pour rendre l'appareil plus performant, de meilleure qualité et plus durable. La difficulté résidait notamment dans le fait de devoir intégrer beaucoup de puissance dans un espace très restreint. En effet, potentiellement, la technologie devrait également être applicable à des appareils de plus petite taille.
Un autre grand défi concernait la gestion de la chaleur et l'efficacité énergétique. L'appareil devrait fonctionner en mode économie d'énergie absolue lorsqu'il est utilisé uniquement comme interrupteur de lumière, mais augmenter sa puissance lors d'applications multimédias. Nous avions besoin d'un nouveau concept de développement pour capturer la chaleur générée pendant de telles pointes de performance, sans recourir à un ventilateur. C'est pourquoi il ne pouvait y avoir de solution prête à l'emploi, et beaucoup plus de travail de développement propre était nécessaire. Nous avons réussi, grâce à cette nouvelle configuration, à réduire le développement de chaleur et donc la consommation en fonctionnement normal. Cela signifie une plus grande efficacité, donc plus de puissance pour une consommation moindre. Et en même temps, plus de réserves de puissance sont disponibles.
Plus de travail de développement propre était également nécessaire pour la construction modulaire à l'intérieur de l'appareil. Avec une modularité technique accrue, nous sommes désormais en mesure d'apporter plus facilement des modifications à la configuration du disque dur ou à des composants individuels tels que le processeur à l'avenir. Même s'il s'agit d'une génération de processeurs obsolète entre-temps. La technologie modulaire garantit donc la plus grande durabilité des appareils mentionnée précédemment.
Quelles ont été les différentes étapes du développement ?
Comme pour tout développement de produit, il y a eu différentes phases. De l'analyse de l'état actuel à la recherche et à la construction de différents prototypes incluant des tests, jusqu'à la production en série. Tout d'abord, nous avons dû déterminer, à partir de sources internes et externes, ce qui fonctionnait bien sur l'appareil actuel et pouvait donc être réutilisé ou ce qui devait être optimisé, en établissant les exigences par ordre de priorité dans un cahier des charges. Sur cette base, nous avons recherché les solutions disponibles sur le marché et ce que nous pouvions développer et fabriquer nous-mêmes. Cela a posé les bases de l'orientation du développement.
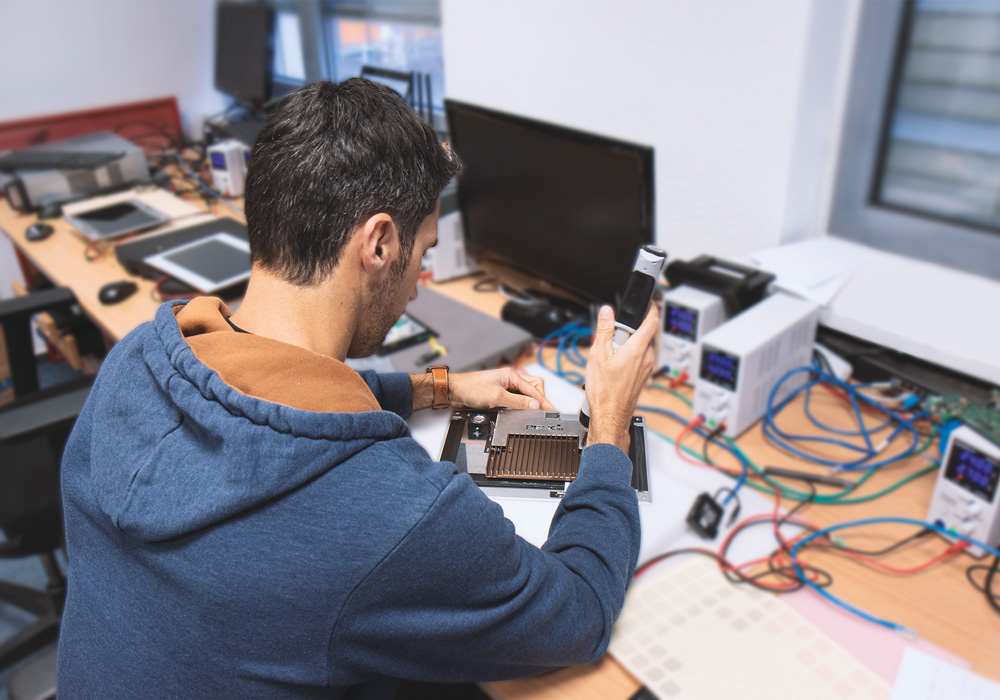
Les choses ont vraiment commencé à devenir intéressantes lors du développement des prototypes. Notre premier prototype différait considérablement de la structure prévue du produit final, mais grâce à différents tests des fonctions fondamentales des composants individuels, nous avons acquis des connaissances importantes, corrigé des erreurs et avons pu commander les premiers composants pour la série.
Notre deuxième prototype s'est approché beaucoup plus de la taille et de la structure du prototype prévu, ainsi que de la position des composants les plus importants. Les erreurs rencontrées lors du premier prototype ont été corrigées, nous avons effectué des tests de charge et des premiers tests CE internes. Finalement, nous avons pu optimiser l'appareil pour la production en série et commander les composants restants. Cela a donné le coup d'envoi à la production en série.
La dernière phase a été lancée par la construction de modèles de pré-série, afin que nous puissions vérifier l'ensemble de la fonctionnalité. Ensuite, après les tests CE internes et externes pour les certifications nécessaires, nous avons donné le feu vert pour la production en série. Ce qui nous a bien sûr rendus très fiers.
Y a-t-il eu des éléments lors de cette transition auxquels vous n'aviez pas pensé et qui ont impacté le calendrier ?
Effectivement. Cependant, pour tout expliquer, cela dépasserait le cadre de cette conversation. Le principal enjeu a été la gestion thermique et l'efficacité énergétique.
En ce qui concerne le calendrier, vous abordez un point sensible. Pour le respecter, nous avons dû redoubler d'efforts. Chaque problème inattendu, chaque résultat de test négatif et chaque demande supplémentaire de la direction pendant les phases de développement mentionnées devaient être compensés par la suite. Il ne faut pas non plus oublier que nous avons pris un risque en optant pour un développement entièrement nouveau. En effet, nous ne savions pas si tout fonctionnerait ensemble comme prévu et si nous obtiendrions toujours les composants nécessaires en quantité suffisante et dans les délais impartis. En fin de compte, cela a été une collaboration intense entre nos développeurs et notre société sœur, PEAK-System Technik. Les collègues là-bas nous ont grandement aidés à atteindre notre objectif. Après tout, nous avons pu puiser dans plus de 30 ans d'expertise interne en électronique et en développement de cartes de circuits imprimés.
Y a-t-il eu des changements au niveau du matériel ?
Comme mentionné précédemment, le panneau a été légèrement modifié sur le plan esthétique, mais seulement de l'avant. Seules des modifications ont été apportées au verre avant : en raison de nouveaux capteurs, quelques nouveaux découpes ont été ajoutés. Un capteur de luminosité régule automatiquement la luminosité en fonction de l'environnement, et un capteur de distance détecte quand une personne s'approche de l'écran et allume automatiquement l'écran. De plus, il y a un voyant LED de notification à l'avant, qui peut être individuellement programmé avec des fonctions. Les ports frontaux, le cadre et les haut-parleurs sont identiques à la version précédente du panneau. Les cadres d'installation précédemment utilisés peuvent également être réutilisés sans problème. Le nouveau dispositif reste compatible avec les anciens cadres en surface ou les boîtes d'encastrement et les kits d'adaptateurs.
Cependant, à l'intérieur, rien n'est resté inchangé. La carte mère a été entièrement repensée, la technologie modulaire offre plus de flexibilité, notamment en ce qui concerne la répartition des ports. Un nouveau processeur est utilisé, et la capacité et la vitesse de la mémoire principale ont été augmentées. Une nouvelle interface USB-C a été ajoutée à l'arrière, et les taux de transfert en gigabits sont désormais possibles via Ethernet. De plus, le transfert de données via LAN, Wi-Fi ou Bluetooth a été mis à jour selon les normes technologiques actuelles.
"Nous avons amélioré les spécifications dans tous les domaines tout en optimisant la gestion de la chaleur. Dans l'ensemble, le résultat de notre travail contribue à une résistance accrue du panneau. Que pourrait-on demander de plus ?"
Et comment le logiciel de visualisation YOUVI a-t-il changé ?
Notre logiciel de visualisation YOUVI se présente désormais dans un nouveau design encore plus clair. Ainsi, il y a un changement de couleur, principalement en bleu et jaune, les widgets intègrent des images et les différents domaines d'application sont désormais encore mieux accessibles via des boutons nouvellement conçus. Bien sûr, la nouvelle version de YOUVI - comme par le passé - peut être utilisée en mode sombre ou clair. De plus, quelques nouvelles fonctionnalités liées à la gestion des utilisateurs, à la climatisation ou encore au son ont été ajoutées.
Êtes-vous content du résultat final de votre travail ?
Absolument ! Nous avons accompli beaucoup de choses dont nous pouvons être fiers : le système est devenu encore plus efficace, car il répond désormais encore mieux aux besoins des clients et à leurs applications. Le logiciel de visualisation a été amélioré, et les performances du panneau ont pu être augmentées de jusqu'à 300 % dans les domaines du disque dur, du processeur et de la carte graphique. Nous avons pu augmenter le benchmark global d'environ 150 %. Nous avons amélioré les spécifications dans tous les domaines tout en optimisant la gestion de la chaleur. Dans l'ensemble, le résultat de notre travail contribue à une résistance accrue du panneau. Que pourrait-on demander de plus ?
Le nouveau panneau est sur le marché depuis le début de 2024 et jusqu'à présent, nous avons reçu des retours positifs constants de la part des clients ! Nous l'avons également constaté en direct lors du salon Light + Building. N'hésitez pas à lire notre article de blog sur Light + Building.